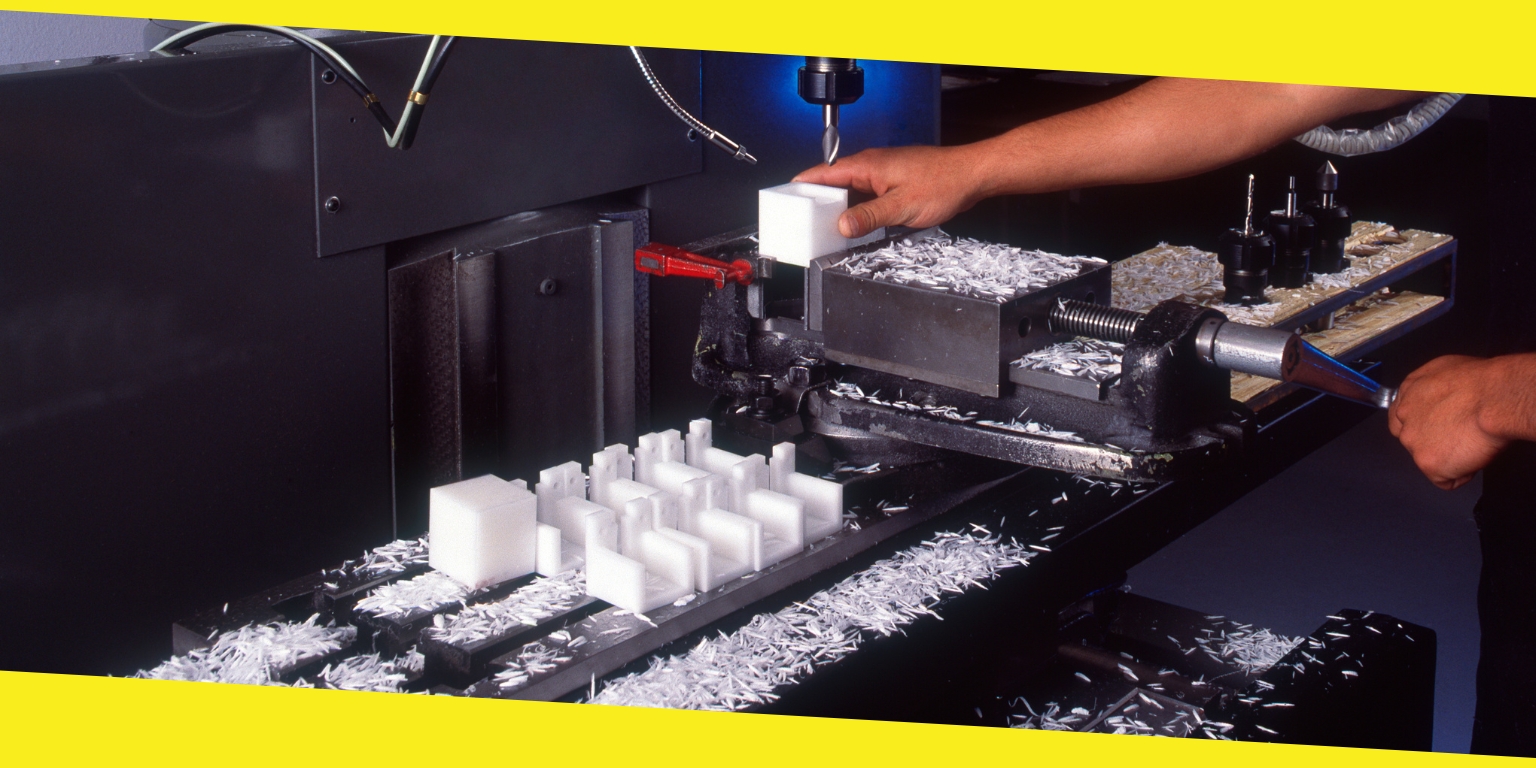
Most plastic manufacturers usually use thermoplastic for plastic molding. Thermoplastics are polymers that quickly melt under high temperatures and cool and harden under cool temperatures. Thermoplastics are different from thermosets which burn if reheated. You, however, can reheat and cool the thermoplastic several times before it’s no more useful.
Thermoplastics are mainly in plastic pellet form when it’s about to be used for plastic molding purposes. You can mix special additives with plastic pellets like colorants, recycled materials, etc.
The most common types of thermoplastics include:
1. Acrylonitrile Butadiene Styrene (ABS)
ABD is a tough and lightweight material. It’s a common material used for plastic molding.
2. Polycarbonates
Polycarbonates are transparent thermoplastics. They’re high-impact resistant and can not break or crack even under high levels of plastic deformation. Most manufacturers use this type of plastic to produce medical devices, mobile devices, and eyewear lenses. It can be used to make bulletproof glass.
3. Nylon
Nylon has unique electrical properties and is solid. It can be used to make sports equipment and even industrial components. This type of thermoplastic can be used for a wide range of applications.
4. Polypropylene
Polypropylene is a flexible material. It also has good chemical resistance and does not leach into food products, making it an ideal choice if you want to manufacture food containers or eating utensils.
5. Polyethylene
Polyethylene is an all-around plastic to use for plastic molding. This plastic material has high flexibility, low moisture absorption, impact resistance, strength, tensile, and recyclability, which makes it a good option for producing plastic containers and bags.
Why is plastic molding good?
1. Mass production
Plastic molding is a fast and efficient production process; using a plastic molding machine, you can manufacture thousands of parts quickly. A plastic molding cycle can take a minute or sometimes less than minutes. And a cycle time is not limited to producing one part of an item; instead, a quick cycle time can have multiple parts with a significant outcome.
2. Less waste
Plastic molding differs from other manufacturing processes, like CNC machining, which shreds plastic from a large block or sheet. However, plastic molding produces less waste.
When using CNC machining, you might begin with a 100g block or sheet of plastic, but after the manufacturing process, the final product may not even weigh up to a few grams. Plastic molding is more conserving and efficient. Using 100g of plastic material, the most you can get is 20g of waste with the plastic molding.
3. Complex parts
Products made using the plastic molding process can be complex, which can reduce the number of separate parts needed to make a single large object resulting in reduced overall production time.
By adding special features such as core pulls and unscrewing fixtures, you can manufacture products with threads or side holes, which means you won’t require any secondary operations compared to other manufacturing processes. You can even mold your company’s brand into the product or item during the production process.